In 2006 GA Smart Building built an 8,000 m² building for Anthogyr, a manufacturer of dental implants. It housed a 5,000 m² high-bay industrial production facility that included a class 1000 cleanroom, and 3,000 m² of offices. An extension of some 1500 m² was then added in 2013.
A high-bay industrial building designed in partnership with the project owner
When GA Smart Building was contacted by Anthogyr to compete in the preparation of a specifications sheet, the dental implant manufacturer was operating on an obsolete site. Its needs were extensive – a dental surgery and head offices were required, and the premises had to be spotlessly clean.
The company opted to build a high-bay industrial production building, which would treat the entire volume of air by oil mist collection. As a result of this exemplary building, completed in just nine months, Anthogyr has achieved growing renown in the world of buyers of dental implants. China, among other countries, imports its implants.
A head office that combines efficiency with well-being at work
GA Smart Building went on to build the company’s head office on the same parcel of land. It is connected to the factory by a connecting building that serves as a secondary entrance for employees, an emergency staircase, and a “work café” designed to foster employees’ well-being.
The office building houses laboratories and orthodontist surgeries as well as a classroom where dentists are trained to put in implants. Preference was given to natural lighting: a series of windows giving out onto the exterior admit abundant daylight into the building.
Efficient building processes by GA
The office buildings feature architectural façade panels, an exterior facing in polished fine gravel, and air treatment modules that fulfil three functions: heating in the winter, cooling in the summer, and air renewal year-round.
The Intertec construction process employed in the high-bay industrial production building, which consists of prestressed concrete produced in the factory, meant that the number of posts could be kept to a minimum. A major constraint was insulation and water-tightness. To cope with this requirement, GA opted for “Alsace II” façades — sandwich panels incorporating insulation, with an outer facing made of washed gravel pavillon and an inner membrane made of concrete.
Lastly, energy efficiency is achieved thanks to Galaxy Pilot®, which can be managed remotely from a smartphone via the application.
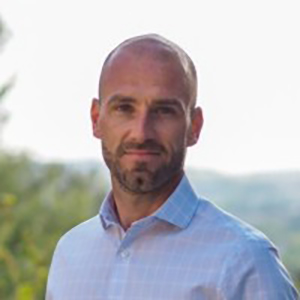
Contact
Thibault Minnaert
Industry Sales Director